Picking
Cos'è il picking?
Il picking è il processo di prelievo e raggruppamento di articoli o merci dal magazzino per gli ordini dei clienti o della produzione. Il dipendente dell'azienda che esegue la procedura di picking è chiamato picker o addetto al picking. La merce viene solitamente prelevata da un magazzino, da un magazzino di picking speciale o direttamente dalla produzione.
Il picking svolge un ruolo importante nella logistica dei negozi online, ad esempio. Questi ultimi devono raggruppare la merce per la spedizione in modo che gli articoli giusti finiscano nel pacco giusto. Per offrire ai clienti il miglior servizio possibile, il processo di picking deve avvenire nel più breve tempo possibile.
Quali sono i sistemi di picking?
Fondamentalmente si possono distinguere due sistemi di picking:
- Da uomo a merce (manuale)
- Merce-uomo (meccanico)
Nel sistema uomo-merce, una procedura statica e manuale, il dipendente si reca in un luogo di stoccaggio per prelevare la merce. Di norma non vengono utilizzati ausili automatici, motivo per cui questo sistema di prelievo è particolarmente adatto a bassi volumi di ordini e ad articoli di peso ridotto. Ciò comporta i seguenti vantaggi e svantaggi:
Vantaggi | Svantaggi |
---|---|
✔ Basso investimento | ✘ Basse prestazioni di picking a causa degli elevati tempi di percorrenza (se non ottimizzati) |
✔ Nessuna dipendenza da macchina | ✘ Punto di prelievo per lo più non ergonomico |
✔ Elevata flessibilità con una movimentazione di magazzino variabile | ✘ Smaltimento dei supporti di carico vuoti richiesti |
✔ Risposta rapida per gli ordini urgenti |
Il sistema uomo-merce viene utilizzato in combinazione con i seguenti tipi di scaffalature:
- Scaffalatura
- Scaffalature mobili
- Archiviazione a blocchi
- Scaffalature a grande altezza (con carrello elevatore per corsie strette)
Nel sistema merce uomo, la fornitura di merci avviene in modo dinamico e automatico. Gli articoli vengono trasportati direttamente al Picker grazie alla tecnologia dei nastri trasportatori. L’addetto al picking prende la merce richiesta da un contenitore nella sua postazione di prelievo, che viene poi trasportata automaticamente alla sua postazione di stoccaggio. In questo modo il dipendente deve percorrere solo un breve tratto a piedi e fa uno sforzo fisico minore. Questo metodo consente di ottenere prestazioni di prelievo relativamente elevate e una bassa esposizione ad errori. I vantaggi e svantaggi in sintesi:
Vantaggi | Svantaggi |
---|---|
✔ Elevate prestazioni di prelievo grazie alla riduzione dei tempi di percorrenza | ✘ Elevati investimenti richiesti per i sistemi di scaffalatura o di prelievo automatici |
✔ Adatto a un'ampia gamma di articoli | ✘ Scarsa flessibilità in caso di utilizzo variabile del magazzino |
✔ Riduzione della predisposizione agli errori | ✘ Pericolo di immobilità in caso di guasto della macchina |
✔ Smaltimento automatico di contenitori | |
✔ Possibilità di progettazione ergonomica del posto di lavoro |
In pratica, il sistema merce-uomo viene applicato, ad esempio, come segue:
- Scaffalatura a grande altezza con sistemi automatici di stoccaggio e prelievo
- Scaffale a flusso scorrevole continuo con trasportatori automatici per scaffalature
- Scaffali paternoster, a torre, a carosello
- Sistema di stoccaggio a prelievo automatico
Quali sono i metodi di picking?
Il prelievo delle merci per gli ordini può essere a una o più fasi. Nel picking a fase singola, ogni ordine viene raccolto singolarmente. Nella variante a due fasi, la quantità totale richiesta di un articolo viene prelevata contemporaneamente per più ordini.
Esistono le seguenti procedure a fase unica:
- Picking parallelo orientato agli ordini
- Picking seriale orientato agli ordini
Il metodo di picking più importante a due fasi è
- Picking parallelo e orientato al seriale
Picking in parallelo orientato agli ordini: più picker, zone separate
Questo metodo di prelievo prevede la suddivisione in aree di stoccaggio diverse. Spesso sono separati spazialmente o strutturalmente. Più picker prelevano contemporaneamente le merci richieste e le riuniscono in un luogo definito (punto di raccolta).
✔ Il principale vantaggio di questo approccio è una significativa riduzione delle distanze e quindi dei tempi di lavorazione.
✘ I principali svantaggi sono la necessità di un punto di raccolta speciale e lo sforzo di coordinamento.
Picking seriale orientato agli ordini: articolo per articolo
Questo metodo di prelievo rappresenta la forma più semplice di raccolta e assemblaggio delle merci. Gli articoli richiesti vengono scelti voce per voce. Gli ordini passano attraverso tutte le zone di stoccaggio interessate, una dopo l’altra. Il passaggio attraverso le aree di stoccaggio viene effettuato da un unico raccoglitore/picker, oppure l’ordine viene trasmesso da zona a zona tra i picker responsabili.
✔ Il vantaggio di questo metodo è che i picker di solito si muovono in piccole aree di stoccaggio, riducendo le distanze. Le stazioni di trasferimento possono essere organizzate con relativa facilità, non è necessario un punto di assemblaggio finale.
✘Lo svantaggio principale è che i pickers delle zone di stoccaggio successive possono essere riforniti di lavoro in modo non uniforme. Questo può comportare sia tempi morti che arretrati.
Picking in serie e in parallelo: prelievo in serie, unione alla fine in base all’ordine
Questo metodo di prelievo si riferisce a una procedura in cui molti ordini vengono combinati e poi prelevati sotto forma di un viaggio di andata e ritorno. Questo giro può includere diverse zone di stoccaggio e essere eseguito in parallelo da diversi dipendenti delle rispettive aree.
Poiché gli ordini vengono prima raccolti per un certo periodo di tempo e solo successivamente rimossi, si parla di picking a due fasi. Solo alla fine viene effettuata la distribuzione degli articoli ai singoli ordini.
Senza l’utilizzo di un software di gestione magazzino adeguato, tuttavia, questa procedura è difficilmente realizzabile dal punto di vista organizzativo.
✔ Il vantaggio di questo metodo è che i singoli punti di stoccaggio devono essere avvicinati meno frequentemente. Ciò comporta una riduzione dei tempi di percorrenza.
✘ Gli svantaggi, tuttavia, sono l’enorme sforzo organizzativo e i tempi di produzione relativamente elevati.
Che ruolo hanno i tempi di picking?
Il tempo di picking è il fattore di influenza più decisivo per quanto riguarda la rapidità con cui la produzione o il cliente ricevono la merce richiesta. Allo stesso tempo, è la leva più importante per l’ottimizzazione dei costi. La tabella seguente mostra come si suddivide il tempo di picking.
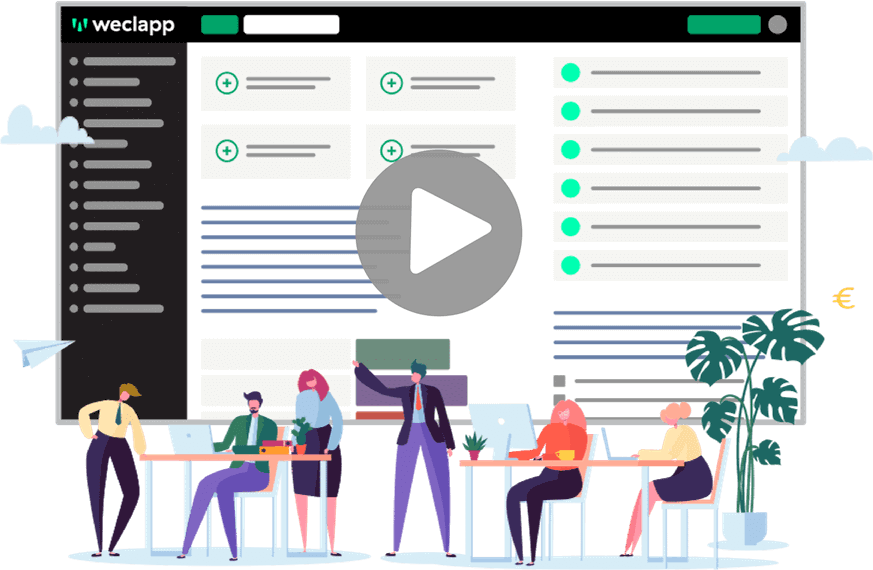
Tempi | Spiegazione |
---|---|
Tempo base | Attività organizzative prima e dopo la commissione, ad es. - Smistamento e lettura delle schede di prelievo - Recupero del dispositivo di prelievo - Restituzione del dispositivo di prelievo - Fornitura di ausili (ad es. pallet, contenitori) - Trasferimento dei contenitori al punto di raccolta o al sistema di trasporto |
+ Tempo di percorrenza | Tempo per la distanza tra due stazioni di prelievo; la registrazione viene solitamente effettuata per articolo. Attenzione: questa è spesso la parte del picking che richiede più tempo. |
+ Tempo di presa | Chiamato anche tempo di ritiro o tempo di prelievo, contiene le seguenti attività: - Rimozione di un articolo dal contenitore di stoccaggio - Mettere un oggetto in un contenitore |
+ Tempo di ripartizione | Chiamato anche tempo ausiliario, comprende le seguenti fasi di lavoro: - Ricerca del luogo di stoccaggio - Formare la "pista" (se necessario) - Confronto, conteggio, controllo - Esecuzione dell'etichettatura - Confermare il ritiro |
+ Tempo morto | Tempo in cui non viene svolto un lavoro produttivo; questo include: - Andare in bagno - Esecuzione di un lavoro di simulazione - Pausa per mancanza di lavoro - In attesa di informazioni o di trasporto |
= Tempo di Picking | Se si misurano accuratamente tutti i tempi individuali e si sommano, si ottiene come risultato finale il tempo di picking. |
Riduzione dei tempi di picking: ecco come
L’obiettivo delle misure di ottimizzazione nell’ambito dell’allestimento degli ordini è sempre la riduzione dei tempi di picking. Più veloce è l’assemblaggio della merce, più bassi sono i costi alla fine. Inoltre, il numero di mancati prelievi e di differenze d’inventario con tutte le loro conseguenze dovrebbe essere ridotto al minimo.
- Ridurre i tempi di percorremza
Ad esempio, una riduzione del tempo di percorrenza può essere ottenuta come segue:
- Disposizione logica delle posizioni di stoccaggio
- Formazione dei dipendenti in modo che conoscano esattamente il layout dei luoghi di stoccaggio
- Utilizzare la strategia dei corridoi: collocare gli articoli di uso frequente all’inizio dello scaffale
- Utilizzare i veicoli per aumentare la velocità
- Utilizzare scaffalature a flusso (senza “vicoli ciechi”)
- Utilizzare un software ERP (Enterprice Resource Planning) o un sistema di gestione merci in grado di creare documenti di prelievo ottimizzati per i percorsi
- Ridurre i tempi di picking
Ottimizzare il più possibile l’altezza e la profondità della presa. In questo caso si devono considerare fattori come il peso, le dimensioni dell’articolo e la sensibilità (ad esempio, articoli pesanti in basso, articoli leggeri in alto).
- Riduzione dei tempi morti
Etichettare gli scaffali in modo che il personale possa individuare facilmente lo spazio di archiviazione. Si consigliano processi di conteggio automatico, soprattutto per gli articoli di piccole dimensioni che vengono prelevati in grandi quantità. Inoltre, riporre gli articoli solo in unità di imballaggio predefinite (ad esempio 5, 10, 50, ecc.) per ridurre le effrazioni.
Quali sono i metodi di picking disponibili?
Oltre al classico picking con le schede di prelievo, si sono affermate una serie di altre procedure (in parte supportate elettronicamente) che vorremmo presentare brevemente di seguito. La scelta della procedura giusta dipende sempre dalle circostanze individuali.
Picking con schede di raccolta (pick-by-paper)
Con questa procedura, il prelievo della merce viene effettuato sulla base di una bolla di prelievo (documento) sulla quale vengono specificati il luogo di stoccaggio, nonché il numero dell’articolo e la quantità. Solo dopo la completa elaborazione del documento, il prelievo viene confermato nel sistema di magazzino.
❗ Tuttavia, l’assegnazione errata dei luoghi di stoccaggio e gli errori di prelievo causano spesso problemi nei processi successivi e anche differenze d’inventario, motivo per cui questa procedura viene sempre più spesso sostituita da soluzioni elettroniche.
Pick-by-MDE (inserimento dati mobile) o pick-by-scan
Il personale di magazzino è dotato di dispositivi mobili per l’inserimento dei dati, che possono essere tenuti in mano o attaccati a un carrello elevatore, ad esempio. Gli ordini di picking vengono trasferiti elettronicamente all’MDE. Se l’MDE dispone di una connessione di rete, può essere alimentato con i dati in modo ancora più flessibile. Oltre al display e alla tastiera, i dispositivi includono solitamente uno scanner di codici a barre o un lettore RFID.
✔ Vantaggi: maggiore flessibilità grazie alla comunicazione in tempo reale, risparmio di tempo, minimizzazione degli errori, feedback diretto al sistema di magazzino.
✘Svantaggio: Una mano del piccker è permanentemente occupata, quindi le prestazioni di raccolta sono inferiori.
❗Principalmente adatto per: merci di grandi dimensioni o pesanti.
Pick-by-voice
Anche questo metodo utilizza un MDE, ma l’ordine viene effettuato tramite un’uscita vocale (cuffie) e il controllo avviene tramite ingresso vocale (microfono). Non sono necessari display, terminali o scanner portatili, il magazziniere indossa solo una cuffia.
✔ Vantaggi: Il picker ha entrambe le mani libere, quindi maggiori prestazioni di prelievo; feedback diretto al sistema di magazzino.
✘ Svantaggi: le cuffie devono essere indossate tutto il giorno, suscettibilità agli errori in ambienti rumorosi, può essere richiesta la capacità di utilizzare più lingue, investimento elevato, costi di formazione elevati.
❗Principalmente adatto per: merci grandi e allo stesso tempo pesanti.
Pick-by-Light
Con il metodo pick-by-light, segnali luminosi vengono utilizzati per indicare direttamente al punto di stoccaggio interessato quali articoli devono essere prelevati per un ordine specifico. Un indicatore di cifre indica la quantità richiesta. Dopo aver effettuato il prelievo, il selezionatore preme un tasto di riconoscimento e lo segnala in questo modo.
✔Vantaggi: non sono necessari altri dispositivi, entrambe le mani libere, nessuna barriera linguistica, addestramento rapido, individuazione molto veloce delle posizioni di stoccaggio, tasso di errore spesso basso, feedback diretto al sistema di stoccaggio.
✘Svantaggi: elevato investimento (installazione dell’elettronica), elevato impegno di manutenzione, il batch picking non è supportato in modo ottimale (ordini diversi difficili da differenziare).
❗Principalmente adatto per: piccoli magazzini, spostamenti veloci/elevata quantità di picking.
Pick-by-Vision
Si tratta di uno dei metodi di prelievo più moderni, che combina i vantaggi di pick-by-voice e pick-by-light.
Tutti i dati rilevanti vengono visualizzati al selezionatore nel suo campo visivo con l’aiuto di occhiali per i dati. È integrato anche un orientamento, che indirizza il dipendente verso la destinazione. Inoltre, per controllare il sistema viene utilizzato un riconoscimento vocale. A seconda del sistema, gli occhiali possono anche svolgere la funzione di scanner di codici a barre.
✔Vantaggi: entrambe le mani libere, velocità di prelievo molto elevata, basso tasso di errore, adatto a diversi tipi di magazzino, feedback diretto nel sistema di magazzino, elevata flessibilità, bassi costi di formazione.
✘Svantaggi: scarsa disponibilità di occhiali dati, hardware non molto robusto, scarsa durata della batteria, è necessaria una copertura WLAN completa.
❗Principalmente adatto per: merci grandi e allo stesso tempo pesanti.
Grafico semplificato dei metodi di prelievo.
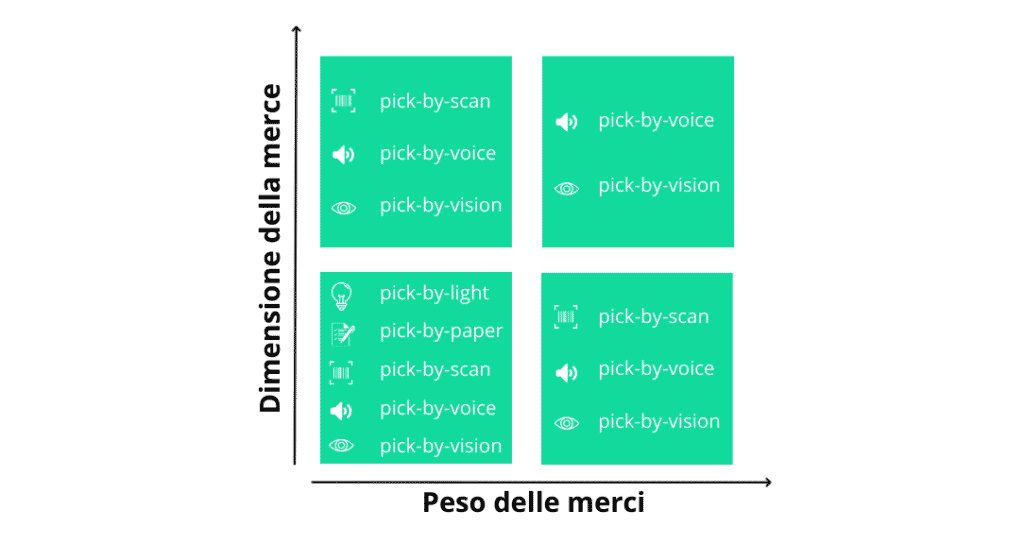
La RFID sta acquisendo importanza nella logistica
L’uso di lettori RFID mobili (RFID=Radio Frequency Identification) consente un prelievo senza voucher e senza interruzioni dei supporti. Non è necessario stampare liste di picking né trasferire registrazioni scritte a mano al sistema di magazzino. Nella logistica interna, l’identificazione a radiofrequenza può essere utilizzata anche per la prenotazione automatica delle merci in entrata e in uscita, ad esempio quando passano attraverso un passaggio dotato di lettori. Interessante anche la possibilità di utilizzare i lettori sotto forma di bracciali o guanti.
✔Vantaggi: picking con entrambe le mani, riconoscimento automatico dei processi, segnale acustico/ottico in caso di errori.
✘ Svantaggi: costi di introduzione relativamente elevati.
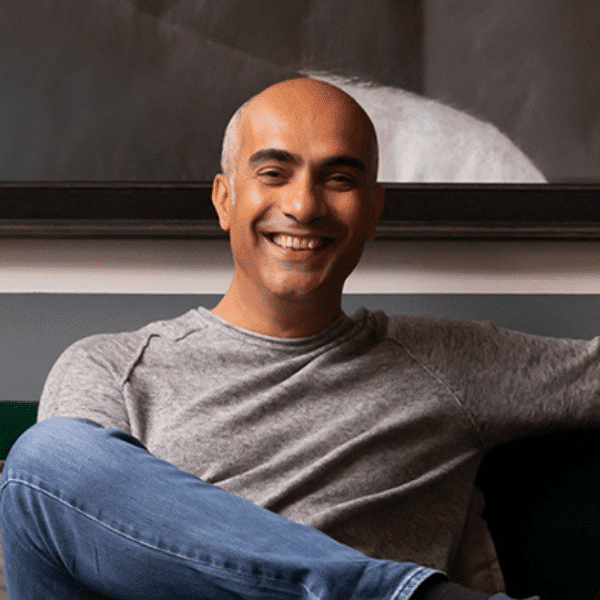
Articoli correlati